Impulse System MPT 700 - DISCONTINUED
- Energy saving
- Reduced pollutant emissions
- Single or two-zone operation
- For continuous controllers, three-point step controllers or manual operation
- Linear ratio between controller signal and burner capacity
- High operating convenience
- Complies with the Low-Voltage Directive 73/23/EEC and the EMC Directive 89/336/EEC
- MPT-C911 drop in replacement available
Learn More:
Description Documentation Applications Specifications
Description
This 19″ module converts a controller signal to pulse cycles for gas burners. This intermittent operation circulates the air in the oven or kiln to achieve uniform temperature distribution and a shorter heat-up time on gas-fired heat treatment ovens.
Eight different operating modes can be programmed on the MPT 700. For instance, it is possible to increase temperature accuracy and achieve controlled cooling via the air valves in heating and cooling mode. The pollutant emissions are reduced by optimum burner operation On/Off or High/Low. The impulse system can control one or two zones with up to eight outputs. One or more burners can be connected per output.
Replacement Available now!
Combustion 911's engineering group has been working to develop a drop-in replacement for MPT 700A. We are ready to unveil MPT-C911!
Click Here for attitional information
Got Parameters? Combustion 911 will set up your MPT-C911 for $100, provided you can supply the parameter set (see below example).
Check out the MPT-C911 manual below for technical information.
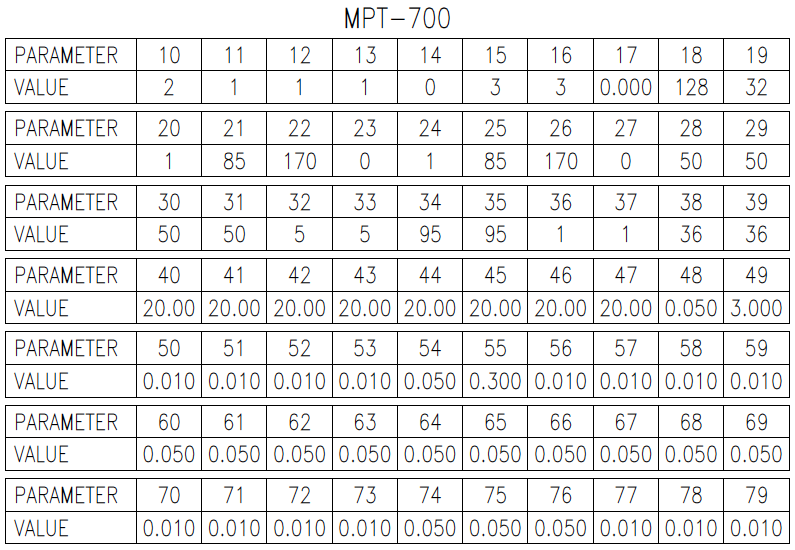
Documentation
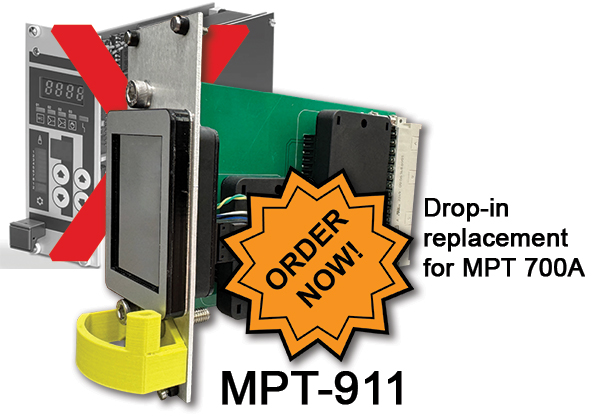
Applications (click on image for close-up view)
Burner Control
The MPT 700 controls the automatic burner control units PFU 760 or PFU 780 with 24 V signals. Automatic burner control units IFS or BCU can also be controlled with mains voltage with the aid of coupling relays.
Heating On/Off
The MPT 700 operates in "Heating" mode. It cyclically switches the ϑ inputs of the automatic burner control units and thus switches the burners on and off.
Heating High/Low
The MPT 700 operates in "Heating" mode. All burners are started centrally via the ϑ input and they burn at min. flow. The MPT 700 controls the air valve inputs and thus switches over to high fire individually for each burner.
Heating and Cooling On/Off
The MPT 700 operates in "Heating and Cooling" mode. A relay determining whether the ϑ input or air valve input of the automatic burner control unit is controlled cyclically is connected to output H/K 1. For heating (= 1), the burners are switched on and off via the ϑ input. For cooling (= 0), only the air valves are switched cyclically with burners switched off.
Specifications
Operating voltage: | 110-240VAC, -15/+10%, 50/60Hz |
Power required: | 10VA, max. 250mA |
Control voltage: | 12-24VDC±10%, max. 1.1A |
CE conformity: | EN 50081-1:1992 EN 61000-6-2:1999 |
Inputs: | 2x 0/4-20mA with common ground, potential-free load approx. 200 Ohm 1x three-point step control input, potential-free1 12-24VDC, load approx. 2700 Ohm 4x binary inputs, common ground, potential-free 12-24VDC, load approx. 2700 Ohm |
Outputs: | 12-24VDC±10%, max. 100mA per channel positive logic : switched +12-24VDC: 10 open emitter outputs |
Electr. connection: | 48-pin contactor, Type F, DIN 41612 |
Design: | open unit European standard size, 100 x 160mm with 50.8 x 128.5 front panel (3 HE, 10 TE) |
Working temperatures: | 0 to +60°C |
Storage temperature: | -25 to +60°C |
Relative humidity: | 0 to 80%, no condensation |
Weight: | approx. 500g |