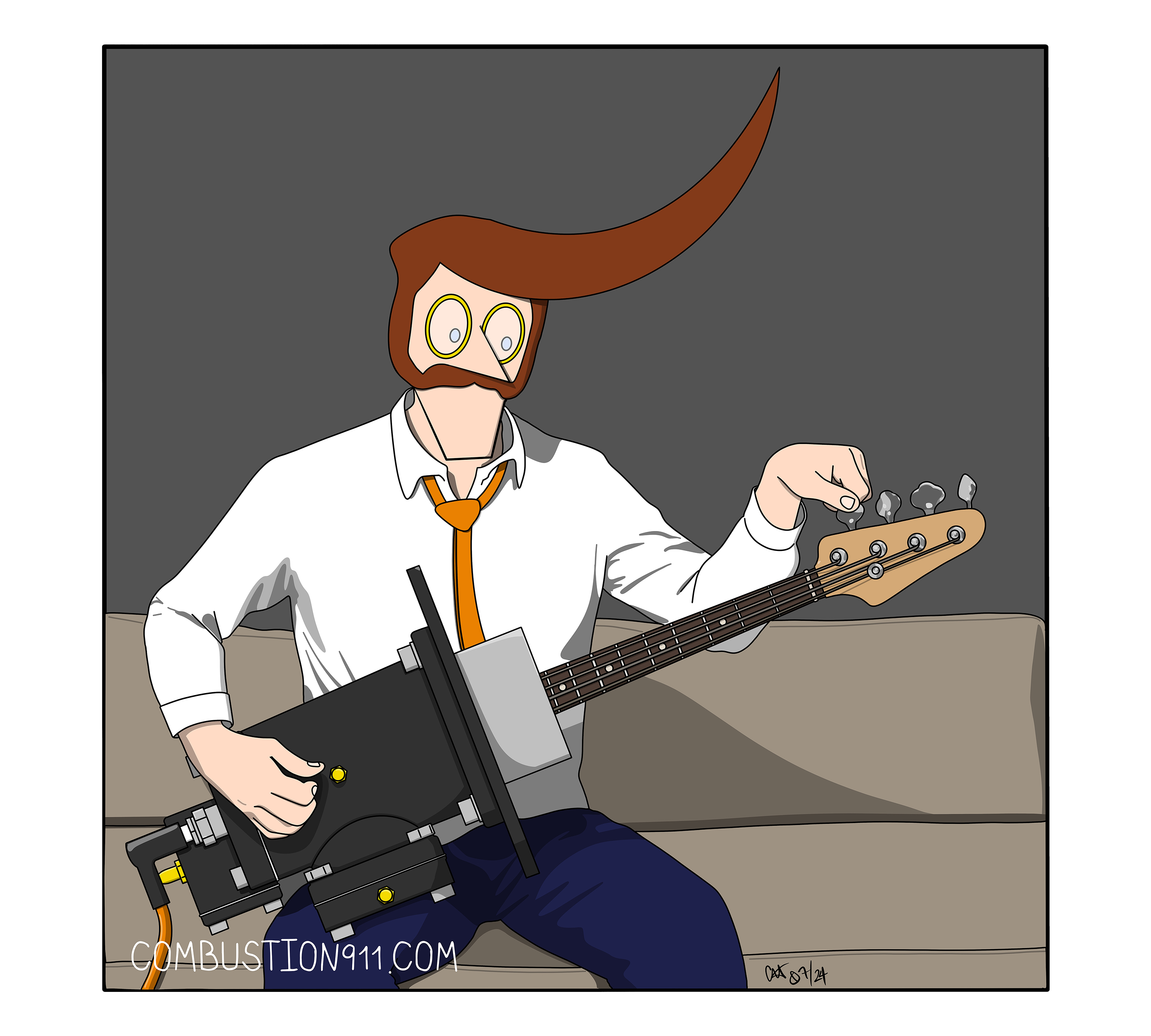
If you’ve ever been to a rock concert, you know that the folks wailing on the guitar need that guitar kept in tune. That’s why they travel with a good guitar tech. The tech makes sure that guitar player can achieve peak performance. Tuning is the key.
It’s the same for combustion systems!
Burner settings migrate over time. Vibration in the system can cause valve set points to change. Shifting environmental factors, like temperature and humidity, can also cause changes in system performance. Well-meaning furnace operators may make ill-advised adjustments while attempting to increase throughput. Replacement parts can change pressure and flow in the system.
Burner tuning is crucial to the performance of any industrial furnace or oven. Burner gas and air settings are published by the burner manufacturer, and the system settings ought to be found on the combustion schematic for the equipment.
What does peak performance of a furnace or oven look like? In a well-designed system, burner tuning is the key to fuel savings (efficiency), reducing harmful emissions, promoting temperature uniformity, and reaching operating temperatures in a timely manner.
Annual burner tuning is recommended for all combustion systems, though some furnaces may require more frequent attention. Note changes in system performance and act accordingly.
You may handle burner tuning in house, through your maintenance department, or you may look outside for a combustion system maintenance partner. Either way, the creation and execution of a reasoned maintenance plan that includes burner tuning is a great way to ensure reliable, repeatable operation, and to identify failing equipment before it becomes a problem.
Are you interested in a maintenance partnership, training for your team so you can handle tuning in-house, or spare parts? Contact Combustion 911 today!