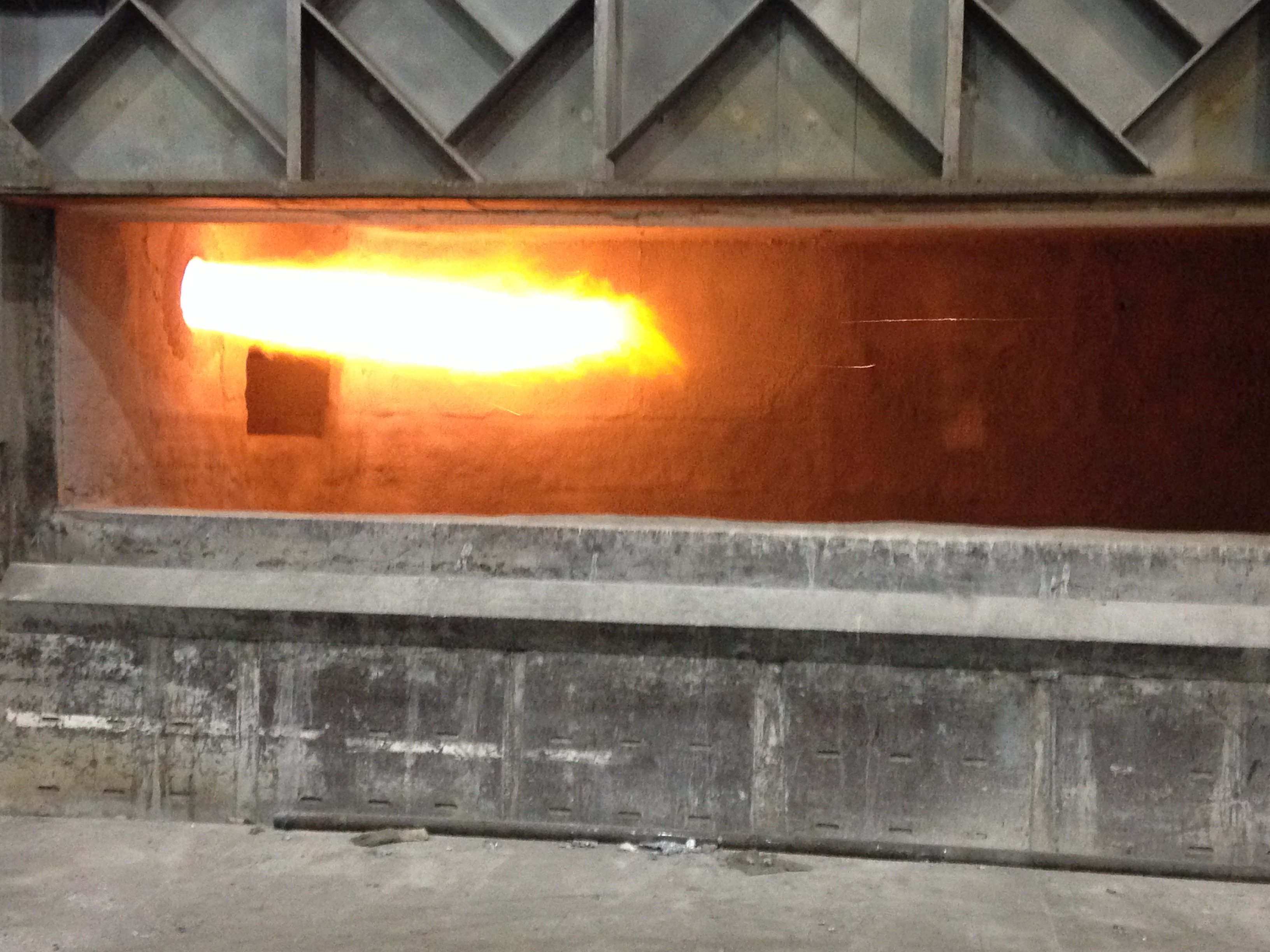
Q: What is an industrial burner?
A: We like to say an industrial burner is just a fancy way of mixing gas and air. This is the primary task of a nozzle-mix burner, because the fuel and air are kept separate right up until the point of combustion. Every manufacturer has a different design for mixing fuel and air. The goal is to provide complete combustion. We aim to consume 100% of the fuel so we are as efficient as possible. Fuel alone is not sufficient for combustion. We also need oxygen, often from air, and a source of heat, usually provided via a spark or pilot flame.
A burner is designed to produce a flame of a specific length, shape, and capacity. These requirements are driven by the needs of the application. Often, this means the burner is firing into a combustion chamber, perhaps alone, or perhaps with several other burners. Combustion often results in heat and light, but it’s the heat we’re most concerned with. Thermal processing is the means through which products are transformed using heat. Metals are formed and shaped, bricks and ceramics are fired, food is cooked, textiles, wood, and paper is dried, etc.
Natural gas is the most common fuel for industrial burners, though propane gas, biogas, and coke oven gas is also used. Part of the push for greater efficiency and lower emissions are the recent initiatives to explore the viability of using pure hydrogen to fuel combustion. Air is often provided to the combustion system using a blower, selected specifically according to the system’s air pressure demands and the elevation of the system’s location. The fuel manifold incorporates filters, isolating shut-off valves, safety shut-off valves, pressure reducing regulators, limiting valves, ratio regulators, and sometimes butterfly valves to manage and control the flow of fuel to the burner. Butterfly valves, linear flow valves, and metering orifices are often used to manage the flow of air to the burner. This is by no means an exhaustive list, in either case.
The burner control unit is an electronic device designed to monitor the safety devices in the combustion system and control the flow of fuel. There are several devices in a combustion system which are part of the “safety chain,” including pressure switches, safety shut-off valves, and flame sensing equipment. Each link in the safety chain must be in place before the burner is allowed to light. The burner controller sends a burner start signal to the ignition transformer, which sends high voltage to the ignition electrode to generate a spark for ignition. While the burner is firing, if any links in the safety chain are lost, the gas valves are closed and the burner is shut down.
Types of Industrial Burners
- Cold air burners: Mix fuel with ambient air. Many cold air burners can also be used with preheated air, which is generated using a central heat exchanger.
- Regenerative burners: Work in pairs, alternately firing and exhausting hot gases which pass through a heat exchange media. The heat is stored and used to preheat the air for greater efficiency and lower emissions.
- Oxy-fuel burners: mix gas fuel with pure oxygen instead of air, which results in primarily carbon dioxide and water vapor emissions.
- Self-recuperative burners: Exhaust hot gases at the same time they are firing. The hot exhaust gas is used to preheat the combustion air, again for greater efficiency and lower emissions.
- Direct-fire burners: Designed to fire directly into the open furnace or oven.
- Indirect-fire burners: Designed to fire into radiant tubes. The heat radiates from the tube to increase the furnace temperature. This method is used in applications where the products of combustion must not come in contact with the work product, or if the work product is a liquid or semi-solid.
- Package burners: typically contain all necessary components for safe operation in one easy to install package. The blower is mounted directly to the burner, as is the fuel manifold. The installer mounts the burner, connects the fuel, and should be ready to start.
- Velocity: Industrial burners: Generally available in high, medium, or low velocity models. Burner velocity is often dictated by the shape of the burner tube (also called a combustor, nozzle, or flame tube). Different velocities are desirable according to the application.
- Premix vs. Nozzle mix: Nozzle mix burners are very popular today for reasons of safety. Pure fuel will not ignite; it requires air, and a source of heat (usually a spark or pilot flame). The fuel and air mix at the nozzle in a nozzle mix burner, just before combustion. Waiting until the last moment to mix the fuel and air help protect personnel and property from uncontrolled combustion (outside of the furnace or oven). Premix burners don’t perform any mixing, and rely on separate mixers to handle this task. There may be one mixer for a bank of premix burners, and a premix system will often contain flame arrestors to protect against flashback, because downstream of the mixer the piping contains a highly flammable fuel and air mixture.
Typical Applications of Industrial Burners
Industrial burners are used in many different processes.
- Heat treatment
- Forging
- Air heating
- Food processing
- Drying
- Galvanizing
- Metallurgy
- Casting
- Manufacturing
For Automation
Please visit olstrad.com to learn more about our automation processes!